Before using silver solder
Clean the surfaces to be mechanically brazed, remove all traces of oxide.
Remove all residue, no foreign particles should be visible.
Provide a clearance of between 0.05 and 0.1 mm in order to optimize the capillary tension.
Respect a regular geometry of the parts to be assembled (fitting and tube in the same axis).
Use only a pipe cutter. Deburr and form a slight chamfer.
Check the regularity of the diameter of the tubes. (Ovalization to be avoided)
No need to use stripper for copper-to-copper joints with Cu-P alloys because it disintegrates the appearance of the joint.
If necessary, apply the flux appropriate to the alloy and to the base metal, preventing it from penetrating inside the tube.
Use of cadmium alloys prohibited on water supply. (*)
- While soldering silver solder
Heat the densest part with a neutral flame, it is the temperature of the brazed part which causes the melting of the alloy.
Avoid excessively long heating periods causing drips and significant oxidation.
Never move parts while brazing.
Never braze oxidized parts.
Never braze parts that are stressed during brazing.
Never solder a tube containing liquid residue.
Never work on a previously brazed part.
Mandatory in the refrigeration industry
Circulate an inert gas (dry nitrogen) in the circuit at a flow rate (30 to 90 l/min).
Use of cadmium alloys prohibited. * Official Journal of the European Communities N° L 186/59 of 12. 7. 91. See "Cadmium" fact sheet.Prefer alloys with 34% silver (534Sn) for "sensitive" bonds and phosphorus copper alloys with silver (105-115) for "basic" bonds. Avoid copper phosphorus alloys WITHOUT SILVER which are economical but intended for plumbing because their elongations (A%) are at least twice as low.
After brazing / removal of flux residues
Remove residue by washing with hot water.
Never cause thermal shock.
Indispensable in the refrigeration industry
Purge lines with inert gas, never use oxygen.
If you follow these guidelines you will be guaranteed:
High resistance of your brazes to mechanical stress (pressure, tearing, torsion, vibration).
Perfect control of the chemical attacks of new fluids
Completely sealed joints, free of porosities.
The know-how of a mastered trade guarantees you the constancy of quality and the flawless safety of your solders.3 Principles to observe
Preparation by careful cleaning of the surfaces to be joined (degreasing, pickling, etc.)
The temperature of the joint must be constant, uniform and slightly above the liquidus point of the filler alloy.
The heating should be as short as possible directed towards the base metal. Rapid cooling is preferable except for cadmium-free silver solders where thermal shocks must be avoidedPreparation tips
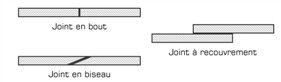
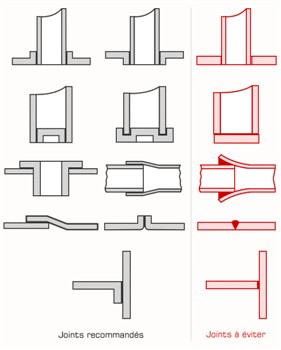
Sources : Comité Scientifique et technique des industries climatiques CHF/CHB.
(*) Sources : J O des communautés européennes. JO N° C8 du 13.01.1990 et additif 26/11/90 JO N° C260 15/10/90 C 129 20/05/91 C 112 07/05/90 JO L 262 27/09/76. JO L 398 30/12/89 JO C 30 04/02/88.